Our industry-leading, high-speed industrial robots include high-payload, extended-reach, ultra-maneuverable seven-axis and unique 15-axis dual-arm robots.
MP3300iec RBT machine controller optimizes baking process
- Endüstriler
- Gıda Endüstrisi için Çözümlerimiz
- uygulamalar
- Taşıma| Paketleme
- müşteri
- Bosso Automazioni
- Ürünler
- MP3000iec Serisi
Fully systematized piadine production
By using a Yaskawa MP3300iec RBT machine controller, the Italian system integrator Bosso Automazioni was able to optimize the performance of a pick-and-place system at a manufacturer of traditional “piadines” or Italian flatbreads. The benefits include lower operating costs, the prevention of downtime and waste, an extended service life for the equipment and thus higher overall profitability.
Described as the “national bread of Ramogna” by Italian poet Giovanni Pascoli, the origin of the piadine dates back to the times of the ancient Romans. Yet even today, the piadine is still well loved by both young and old alike. Over the years, piadine production has spread across the borders of Italy and seen rapid international growth. According to data from the Consortium for the Promotion and Protection of Piadina Romagnola, piadine production increased further still in 2020 as a result of the Covid-19 pandemic, reaching an impressive 22,030 tons. This corresponds to an increase of 23.3% compared to the previous year. However, it would not be possible to satisfy the growing demand in the market without well-functioning production lines.
An underperforming pick-and-place system
It was for this reason that a piadine production plant in the province of Rimini approached system integrator Bosso Automazioni (www.bosso.it). Since 2001, the Rimini-based system integrator has been designing custom machinery and working in partnership with Yaskawa to implement its innovative ideas.
It was this close collaboration that enabled the company to redesign the plant's pick-and-place system, which is used to stack the piadine ready for packaging. The previous system was severely outdated, based on an obsolete concept and included non-industry-standard components (such as cameras).
With two delta robots, each guided by a separate controller with MECHATROLINK-II interface and Sigma-7 servo motors, the production line had never achieved the desired results. Despite adding an extra robot, the plant was still dealing with low efficiency, inadequate product holding fixtures, frequent component failures and overloading of amplifiers. With the increase in production rates required to meet peak demand, these issues were only going to get worse.
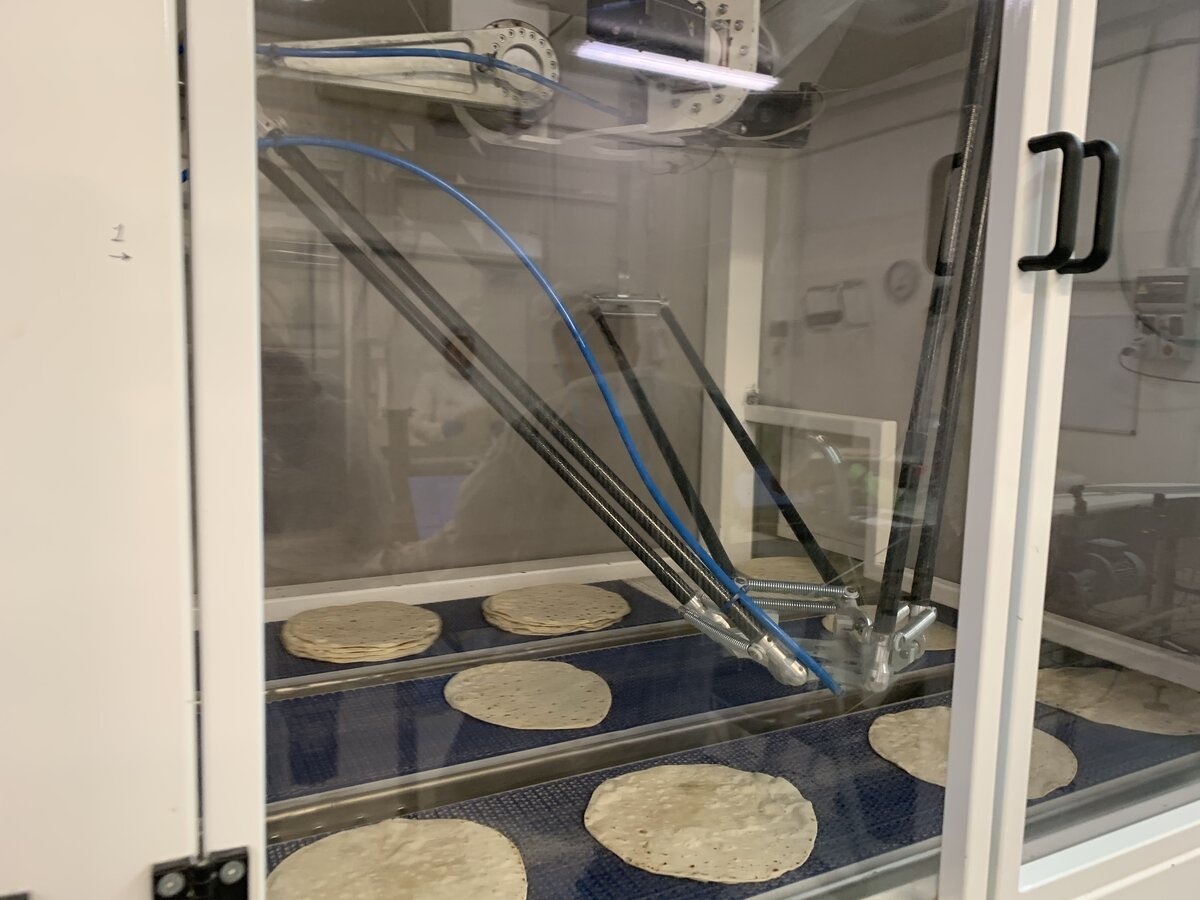
Sophisticated technical requirements
The end customer was therefore very clear in its objectives: the elimination of control, reliability and cycle issues, an increase in productivity to 85 piadines per minute (5,100 piadines per hour), a reduction of reject products to less than 3%, improvement of the service life of the equipment used, improved motor calibration and enhanced quality of movement sequences to prevent or reduce servo motor failures. In addition, they wanted to minimize the number of changes to the existing system as much as possible.
This was a seriously complex task. The piadine has to be picked up and deposited between counter-rotating conveyor belts. The system also requires a high degree of variability, both in terms of shape and positioning. As a result, conveyor tracking functions must be used on the moving belts to pick up and deposit the products. After undergoing a long baking process, the piadines exit at irregular intervals for subsequent cooling. The customer then had a further requirement – the packaging must be designed to hold a varying number of products, yet still look aesthetically appealing. A piadine with the traditional dark roasting marks must be positioned at the top of the packaging so it is the first thing the customer sees.
To control the overall process, a solution was required that could interact with a large number of components (including some that were non-industrial). It was decided that the MP3300iec RBT machine controller would be integrated into the firmware of the control mechanism. The concept of using a single controller for the entire system was adopted, allowing for better control of the interacting functions of the components.
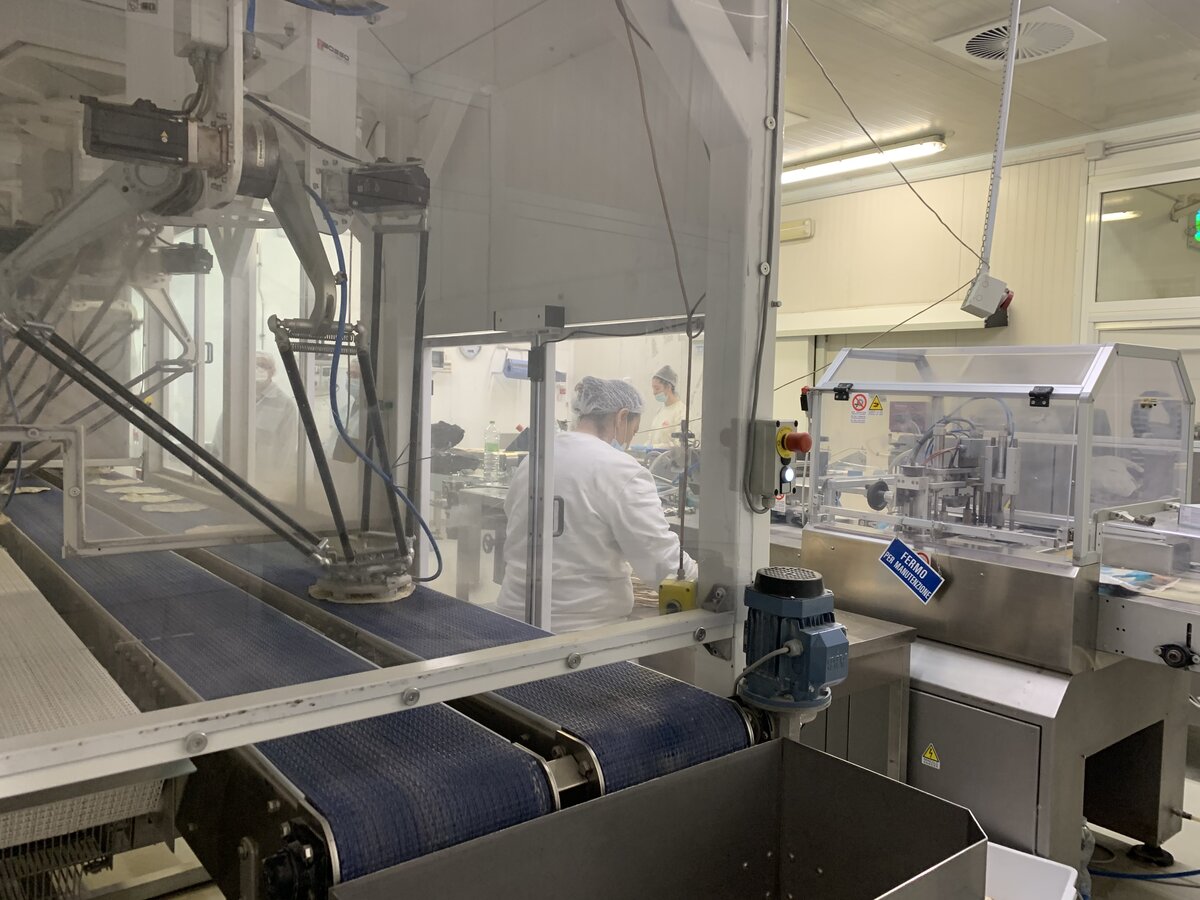
Simulation during ongoing production
However, there was yet another complicating factor. Since the end user is a supermarket supplier working three shifts per day, the production line could not be interrupted during the migration to the fully integrated Yaskawa solution.
The dynamics of the machine were fairly complex, due to both the high level of variability and the use of a camera (instead of a conventional vision system). The camera was also positioned outside of the robot's workspace, which made calibration even more difficult.
Furthermore, the system included third-party robots. After taking these factors into consideration, the MP3300iec RBT was selected as the machine controller. Since it was not possible to carry out a practice run beforehand and production could not be stopped, the Yaskawa team decided to test the efficiency of the sorting algorithms in a simulation on the cell's HMI panel.
The idea was to develop and test the application on the simulator and then switch from the simulation to the real machine. The results were impressive. The tailor-made simulation made it possible to optimize load management and quickly adjust the speed of the robots. Once a real cell was in operation, the simulator allowed the process to be visualized in real time. The flexible algorithms developed for the application were also able to seamlessly manage the characteristic irregularity of the incoming products. The goal of stacking around 6,000 piadines per hour was achieved and the percentage of rejects was reduced to zero.
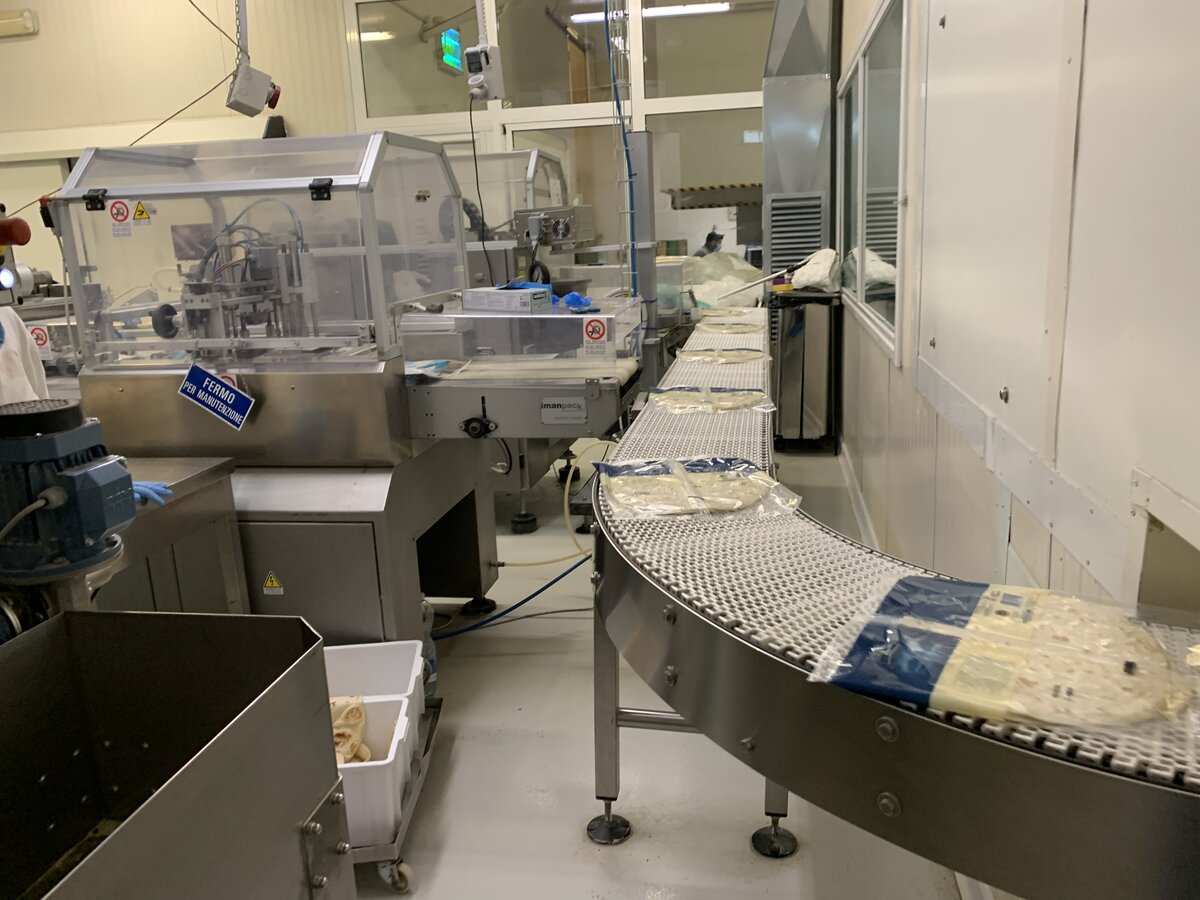
Success factors and results
Yaskawa's expertise in data collection, risk analysis and project management was key to the success of this project. The result in terms of energy efficiency was also of great importance: Whereas each Delta robot was originally controlled by a separate controller, there is now a single controller for the entire solution. The cumulative load has been reduced to 55% of its original value and the servo motors have been downsized from 1.0 kW to 750 watts.
By optimizing the movement sequences, the company made it possible to increase the average service life of the equipment, reduce operating costs, reduce downtime and reject products, and thus make the plant more profitable overall.