Our industry-leading, high-speed industrial robots include high-payload, extended-reach, ultra-maneuverable seven-axis and unique 15-axis dual-arm robots.
ADM Automation & Engineering increases efficiency in MALZERS bakery
A masterpiece for the master baker
When an enticing aroma wafts through the neighbourhood in Bochum, Essen or Mülheim it is usually due to a nearby branch of Malzers. The family-run business, now in its fifth generation, ensures that the Ruhr region is supplied daily with fresh rolls, breads and cakes. Recently, the master bakers have received the support of six Motoman industrial robots from Yaskawa.
- Endüstriler
- Gıda Endüstrisi için Çözümlerimiz
- uygulamalar
- Pick & Place
- Material Handling
- müşteri
- ADM Automation & Engineering
“Although automation has already arrived in the bakery industry, the use of robots is not yet the standard for medium-sized companies. Malzers bakery is a pioneer in this field,” says Peter Dunschen, Founder and Managing Director of ADM Automation & Engineering in Warburg, East Westphalia, about his customer. His company has been designing and programming systems for over 20 years, mainly for the use of large bakeries and companies in the fields of container glass, transport and packaging.
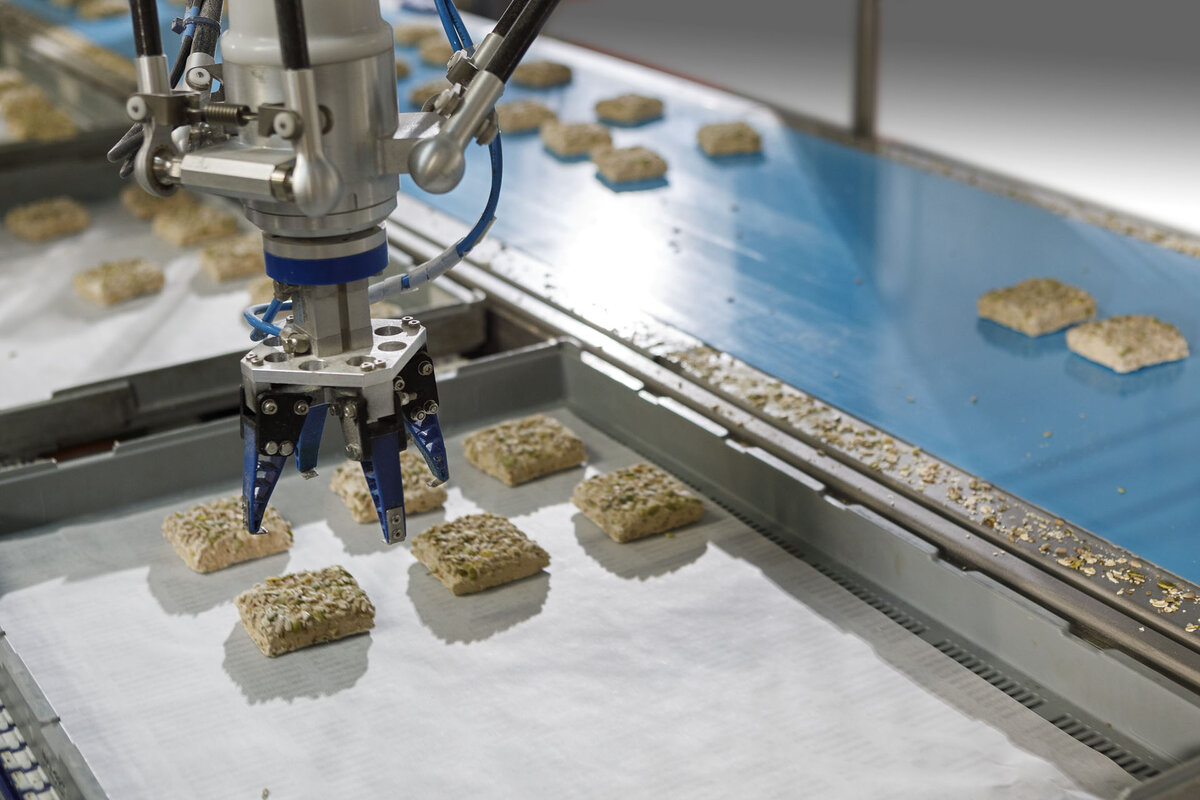
Expansion as a driver for automation
With the company’s expansion – more than 150 stores are supplied daily – a desire to optimize production processes arose at Malzers bakery. Managing Director Christian Scherpel and Björn Hennig, Technical Managers at Malzers, turned to Peter Dunschen, who recommended the use of robots. Dunschen recalls: “We contacted a well-known manufacturer of industrial robots, but our request was not answered satisfactorily. In all truth, we were very badly advised. Through our network we then came upon Yaskawa, and after a short time it became clear: With this partner, we can and want to implement the plant for Malzers.”
Specifically, it was a production line that automatically loads baking trays and sheets with frozen bread dough. Until now, this was done manually by Malzers employees. While the trays go directly into the production process at the main site in Gelsenkirchen, the sheets are delivered to the branches, where the dough is baked on site to make fresh rolls.
As an automation specialist, ADM has been increasingly involved in the field of robotics in recent years. “We have already been able to develop solutions with some customers who have reached their limits with other system providers,” Dunschen proudly says. With the order from Malzers, however, he was also taking a step into unknown territory: “We only started mechanical engineering in 2022, when we took over the employees from another company. The plant for the Malzers bakery was our masterpiece – the first to be implemented in our newly built premises!”
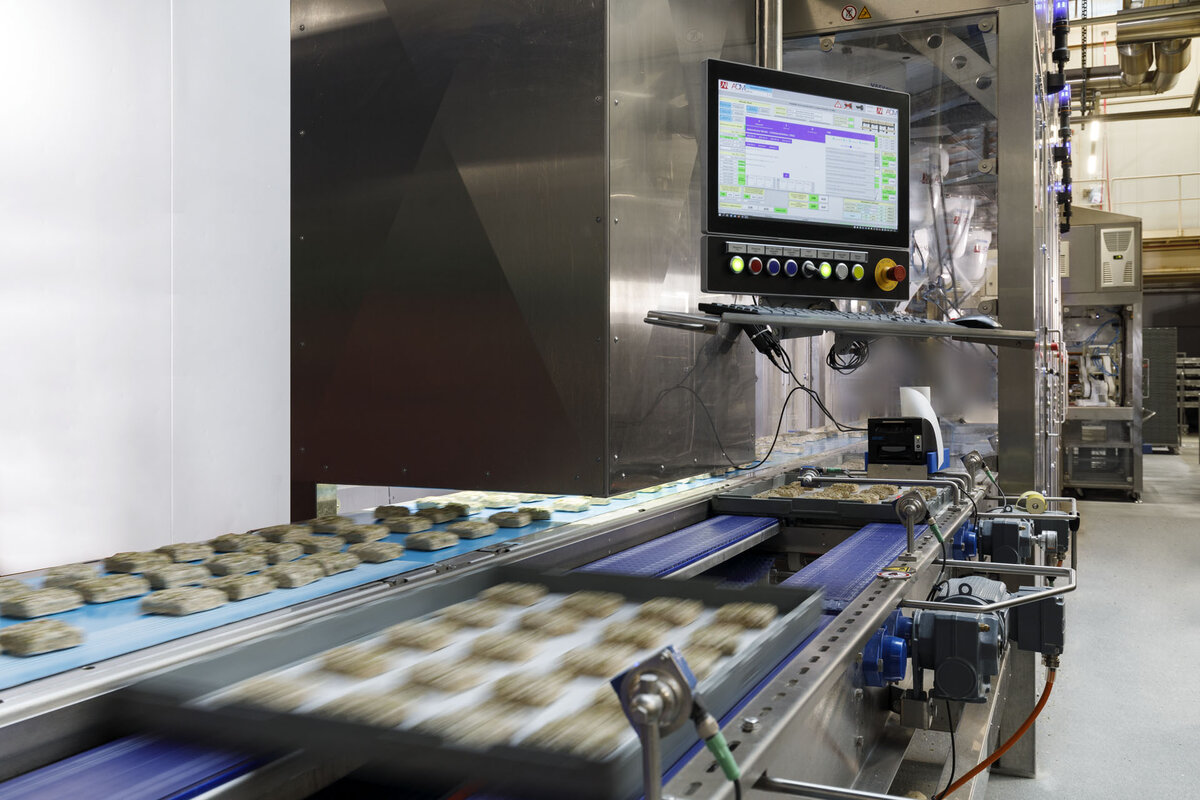
Picture: Expansion through automation: a production line at Malzers’ bakery automatically loads frozen bread dough pieces onto baking trays and sheets.
Special challenge in the food sector
In the solution proposed by ADM for Malzers bakery, robots take over three steps – depalletizing, inserting the baking paper and loading the dough pieces onto trays or sheets.
To ensure safety and quality, robots that come into direct or indirect contact with food must be specially adapted. Among other things, specifications such as GMP guidelines (Good Manufacturing Practice) must be complied with, e.g. in terms of materials, cleanability and hygiene design. Yaskawa already offers food-safe versions of its Motoman robots, with certified food fat in the gearboxes, improved airtightness and special paint finish.
Picture: Four Motoman MPP3Hs load bread rolls onto the trays and sheets; these are then transported on a conveyor belt from the opposite direction.
Six robots take on three work steps
After an employee has moved the trolleys with trays or sheets to the cell, a handling robot is placed on the conveyor belt. One of the customer’s conditions was that there should be no interruption in operation when changing the trolleys. ADM chose a Yaskawa Motoman GP180-120, a flexible 6-axis robot, and positioned it centrally in front of the conveyor. This allows the trolleys to be docked on the belt from both sides. Once one side has been depalletized, a safety fence is raised, and the robot turns to the trolleys on the other side. An employee can remove the empty trolleys and replace them with full ones. The robot individually picks up 400 trays or 1,000 sheets per hour (two per cycle) and places them on the belt; the trays are then sucked in and the sheets clamped.
The central positioning and the size of the trolleys called for a robot with a relatively large reach. In addition, the gripper – at around 90 kg – is not exactly a lightweight. With a payload of up to 120 kg and a working range of up to 3.0 metres, Yaskawa’s Motoman GP180-120 proved ideal for the restricted space between the trolley and belt.
Picture: A Motoman GP180-120 handling robot picks up 400 trays or 1,000 sheets per hour and places them on the belt.
Paper insertion by a Motoman MPK2F
A Motoman MPK2F then lays the baking paper in position. Depending on whether it is a tray or board, a different paper format is necessary: the paper carts are coded accordingly. The gripper with suction unit is suitable for both paper types, so no setup time is required. When a paper cart is empty, the MPK2F automatically switches to the next one and the first can be refilled.
The 5-axis Motoman MPK2F is a compact, high-speed pick & place robot with a payload of 2 kg and a reach of 900 mm. “Previously, we experimented with a 3-axis Delta Picker and a Motoman GP7. But only the MPK2F was able to satisfy our speed requirement of 1,000 sheets per hour,” Dunschen explains. The MPK2F has a special wash-down paint finish and was specially developed for use in the food industry.
Picture: With a capacity of 1,000 sheets per hour, this Motoman MPK2F caters for baking paper in two different formats.
MPP3H: Designed for the food industry
In the last step of work, four Motoman MPP3H come into play. They load the trays or sheets with bread rolls arriving on a second conveyor belt from the opposite direction. ADM chose the compact 4-axis high-speed robots – likewise certified as standard for use in the food industry – for one reason, as Dunschen explains: “Each MPP3H carries out 80 picks per minute.” This speed is made possible by the high torque of the fourth axis, the so-called handwheel axis.
The different loading configurations presented a challenge, Dunschen explains: “The stores order different quantities of different rolls, and we have to take this into account.” Here, ADM benefited from its long-standing experience in automation. Via a computer interface, the Delta Pickers receive the calculated loading configuration per tray, so that each store’s specification in terms of variety and number of rolls can be met. At the end of the process, the trays and sheets are manually loaded onto trolleys, and prepared for delivery or baking.
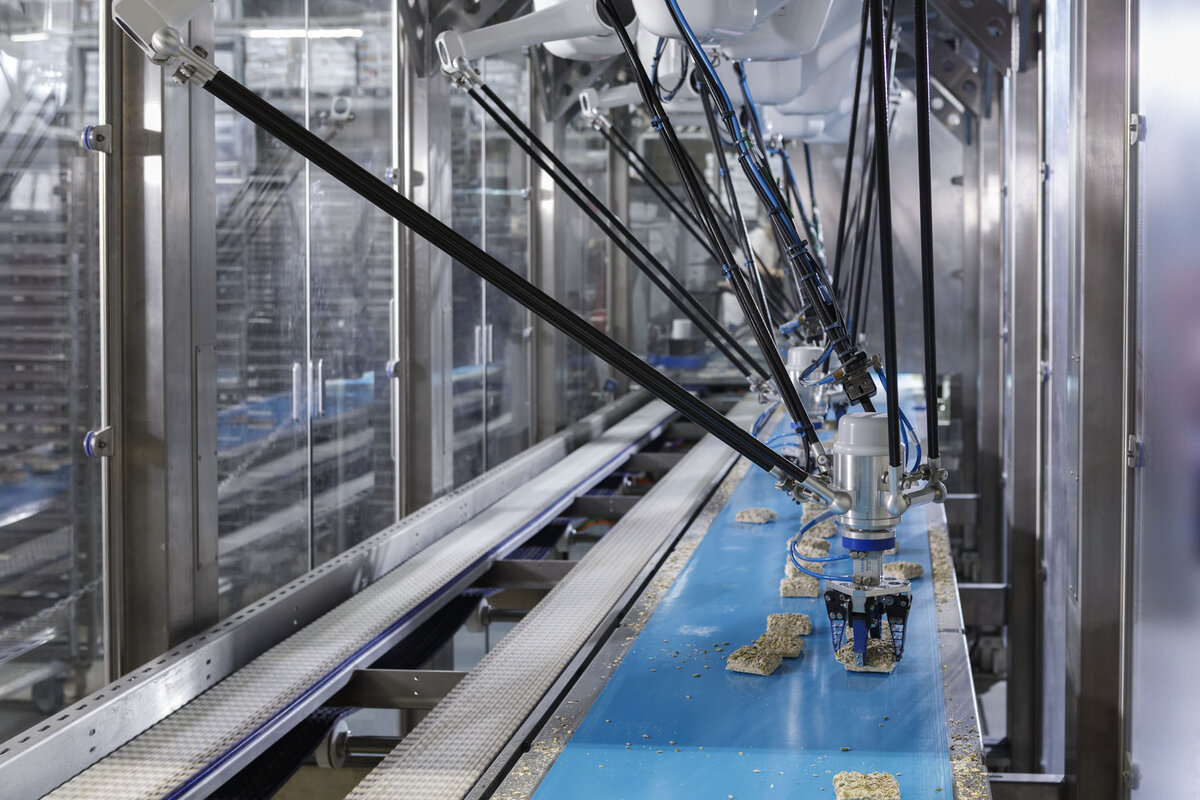
Image: “Each MPP3H carries out 80 picks per minute.”
Potential for further cooperation
When it came to the acceptance of their first plant, he and his team were already a little nervous, Dunschen admits. But after two hours it was clear: Malzers’ requirements were exceeded. Instead of the required 8,000, the plant processed even 9,000 dough pieces per hour. The acceptance test was almost complete, and since then the production line has run smoothly,” says a satisfied Dunschen.
Credit must also be ascribed to Yaskawa, he stresses: “We received every conceivable support in this project. Our contact person was always available to us, advised us and dealt intensively with our project.
From the first contact it was clear: Yaskawa strives for a real, long-term partnership, not a quick deal. For us no other supplier is worth considering!”
Both Malzers and ADM see further potential in the automation of the bakery. For example, robots can insert the loaded trays or sheets into the trolleys, or do the preparatory work – remove the dough pieces from the bags. “We have already talked about this, but we haven’t thought of a concrete concept yet,” says Dunschen.
Meanwhile, ADM is already working with another bakery on the automation of its production. Here again, robots will be used for the first time. From Yaskawa, of course.
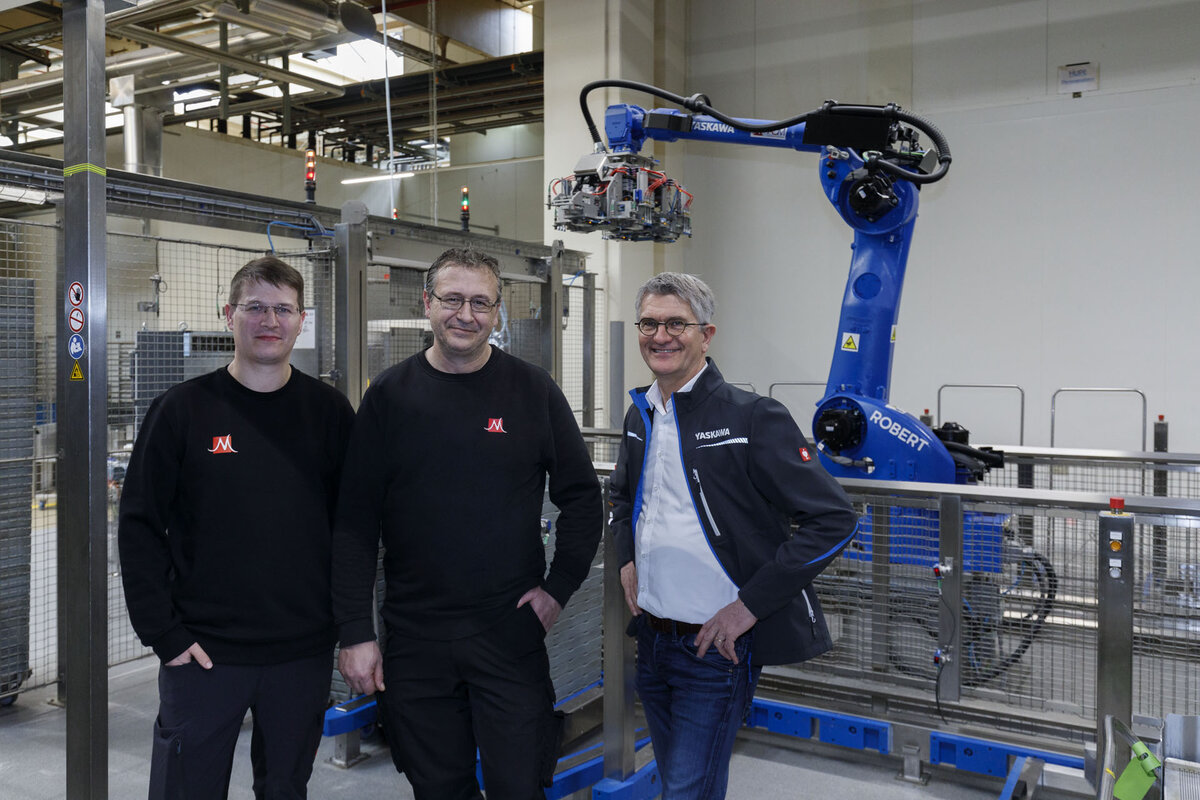
Picture: Robotics experts among themselves (from left): Steffen Wöstefeld and Peter Dunschen from ADM with Stefan Westermann from Yaskawa.
Author:
Stefan Westermann, Sales Manager, Yaskawa Europe GmbH, Robotics Division, DE-Allershausen
Contact for readers’ enquiries:
Tel.: +49-8166-90-0
robotics@yaskawa.eu
Contact for the press:
Marion Annutsch
Marketing / PR / Communications
Yaskawa Europe GmbH
Tel.: +49-8166-90-0
marion.annutsch@yaskawa.eu
www.yaskawa.eu.com
Source for all pictures: Yaskawa Europe